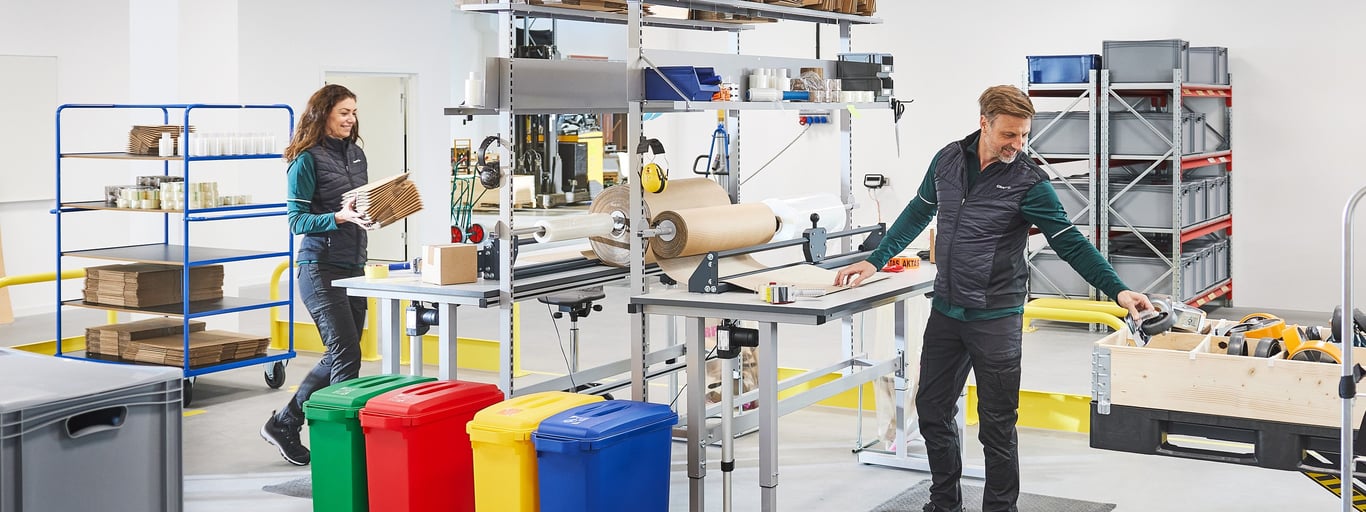
5S-menetelmä: Paranna työtehoa järjestelmällisyydellä
Turvallisempi, nopeampi ja kustannustehokkaampi tuotanto – onko se mahdollista? Toisen maailmansodan jälkeisenä aikana japanilainen Taiichi Ohno kehitti Toyotalle strategian, jolla oli merkittävä vaikutus koko teollisuuteen. Tänään voimme soveltaa tätä strategiaa kaikkeen suurista organisaatioista paikalliseen tuotantoon – jopa työpöydän sotkuihin. Tässä opit ymmärtämään ja onnistumaan 5S-menetelmän avulla, joka on yksi keskeisistä työkaluista arvon virtaamisen varmistamisessa!
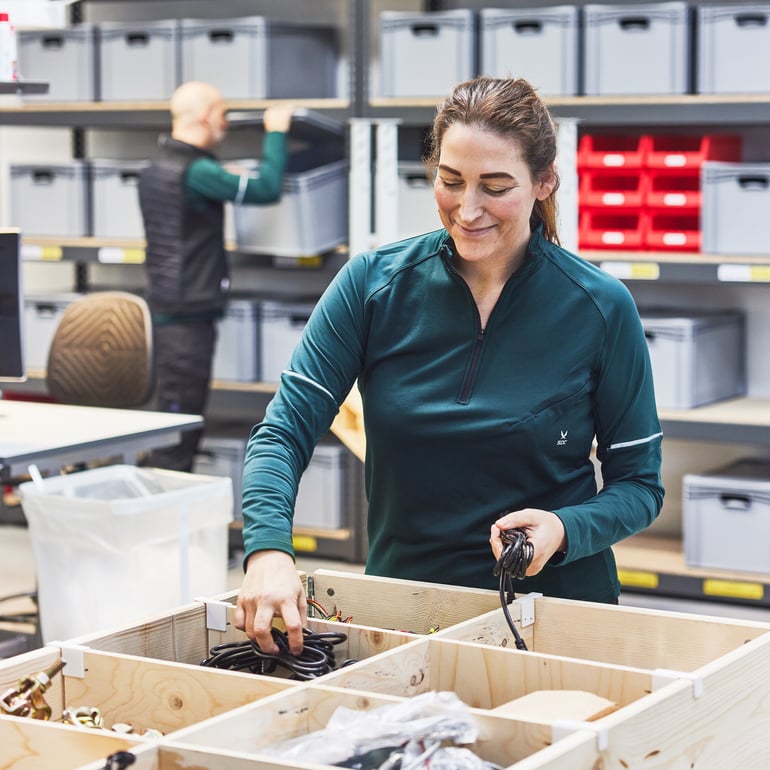
Mitä 5S tarkoittaa?
Seiri. Seiton. Seisō. Seiketsu. Shitsuke. Jos et ole sujuva japanin kielessä, voit käyttää seuraavia suomenkielisiä vastineita:
- Sortteeraus
- Systematisointi
- Siivous
- Standardisointi
- Seuranta
Jokainen "S" edustaa menetelmän viiden vaiheen ensimmäistä kirjainta. Helppo muistaa, ja menetelmä itsessään on yhtä yksinkertainen!
5S-menetelmän perusperiaatteet
Sortteeraus: Poista tarpeettomat esineet työpaikalta
Karsi pois kaikki tarpeeton. Tämä voi tarkoittaa työkaluja tai laitteita, joita ei koskaan käytetä ja jotka vievät turhaan tilaa, tai kuluneita työkaluja, jotka tulisi korvata. Inventaarion avulla vähennät hukkaan menevää aikaa ja poistat häiriöitä tai esteitä, jotka voivat aiheuttaa onnettomuuksia.
Systematisointi: Aseta esineet helposti saataville ja löydettäväksi
Järjestä tavarat loogisen ja helposti ymmärrettävän järjestelmän mukaan. Tämä voi tarkoittaa esimerkiksi hyllyjen ja laatikoiden merkitsemistä tai työpisteiden järjestämistä paremman työvirran saavuttamiseksi. Tavoitteena on, ettei aikaa mene hukkaan työkalujen etsimiseen tai odottamiseen.
Siivous: Pidä työpaikka puhtaana
Pidä työpaikka ja sen laitteet siisteinä. Mieti esimerkiksi, mitä jätät seuraavalle työvuorolle tai henkilölle. Säännöllisellä puhdistuksella voidaan havaita myös poikkeavuuksia, kuten kuluneita laitteita tai rikkoutuneita koneita. Toisin sanoen, kyse on siitä, että pidetään asiat hyvässä kunnossa.
Standardisointi: Luo rutiinit ja aikataulut työpaikan järjestyksen ja siisteyden ylläpitämiseksi
Arvioi tuloksia esimerkiksi mallien, protokollien tai kaavioiden avulla, jotka auttavat luomaan rutiineja arkeen. Tämä vaihe on tärkeä johdonmukaisesti hyvien tulosten saavuttamiseksi. Tässä voit huomata, ettei aiemmin luotu järjestys toimikaan odotetusti.
Seuranta: Säilytä ja paranna standardeja noudattamalla aiempia vaiheita
Tavoitteena on vakiinnuttaa toimivat työprosessit työpaikalla. Tämä edellyttää, että protokollia ja aikatauluja noudatetaan ja toteutetaan oikein. Tässä vaiheessa huomaat, mitä tarvitaan sujuvan työnkulun varmistamiseksi, kuten työntekijöiden koulutus, tiheämpi seuranta tai parempi palaute.
Miten 5S kehittyi kehitystyön työkaluksi
5S-menetelmä on lähtöisin Japanista ja kehitettiin yhdessä Toyota Production Systemsin (TPS) kanssa. Toyotan tuotannon johtaja Taiichi Ohno loi strategian tuotannon hukan poistamiseksi. 5S perustuu tehokkuuteen ja rakenteellisuuteen, ja siinä painotetaan tuloksia sekä jatkuvaa parantamista. Menetelmä täydentää hyvin Lean Managementia.
Vähemmän kustannuksia, sama laatu
5S-menetelmä luo perustan rutiineille, jotka voivat tehostaa kaikkia liiketoiminnan osa-alueita. Karsimalla tarpeettomat asiat saadaan enemmän aikaa keskittyä olennaiseen, ja työnkulku sujuu luonnollisesti paremmin. Tavoitteena on saavuttaa johdonmukaisia, laadukkaita tuloksia niin tuotannon kuin suorituskyvyn osalta. Kuitenkin, 5S on pitkäjänteinen strategia – suurin hyöty tulee vasta ajan kanssa.
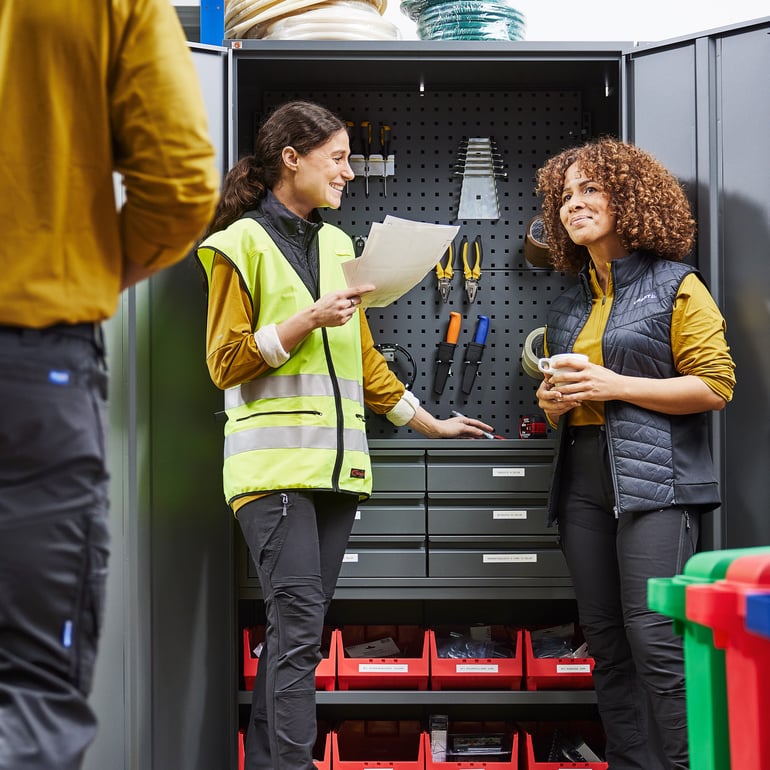
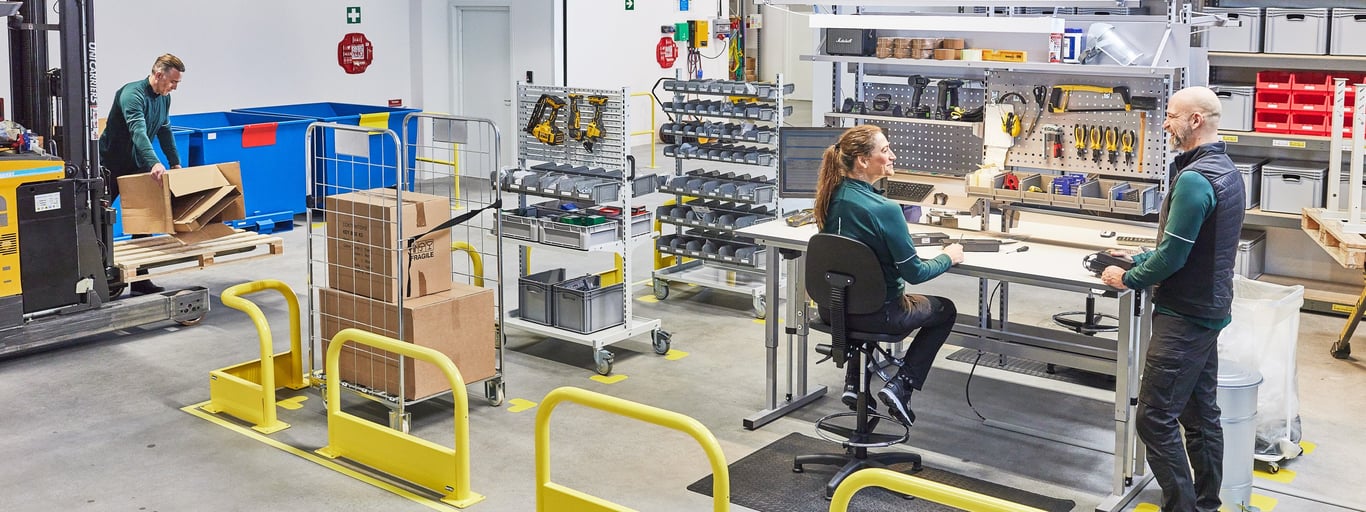
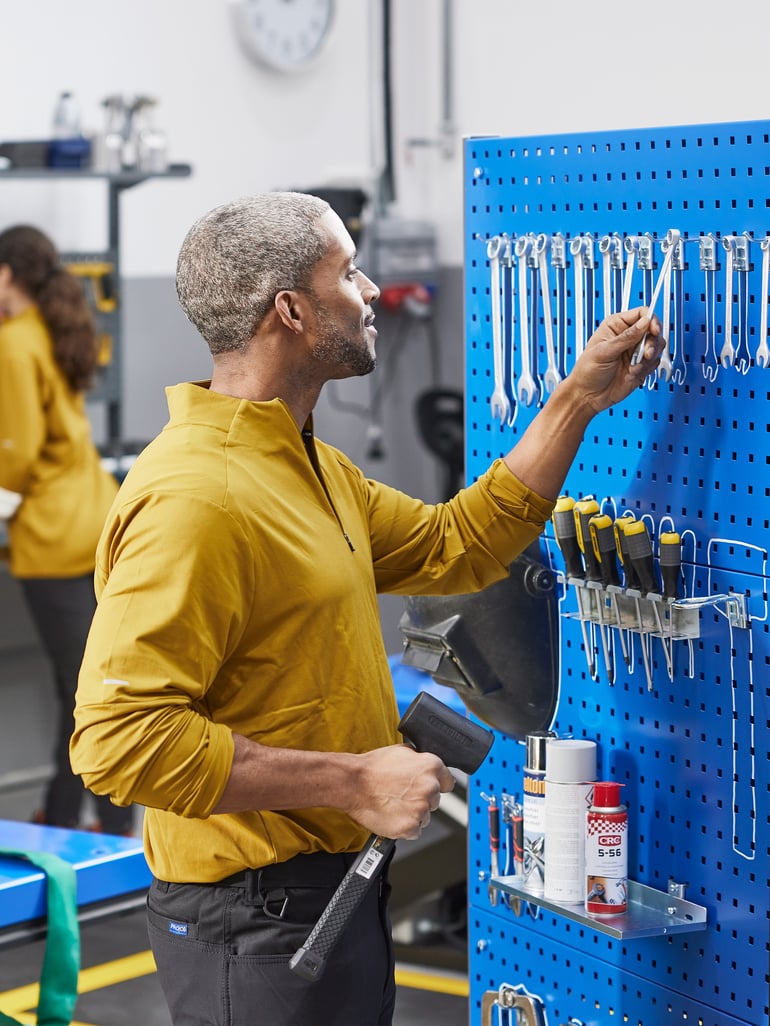
Tehokas tapa vähentää riskejä
5S ei ole ainoastaan työkalu järjestyksen luomiseksi, vaan se lisää myös turvallisuutta työpaikalla. Selkeät merkinnät, kyltit ja varastohyllyjen rakenne auttavat esimerkiksi vähentämään turhaa liikkumista työpisteiden välillä. Säännölliset koneiden ja työkalujen tarkistukset voivat myös paljastaa vikoja, jotka voisivat johtaa onnettomuuksiin.
Tehokas tapa parantaa työn tuottavuutta
Aika, joka kuluu tavaroiden etsimiseen tai odottamiseen, on myös hukkaa. Analysoimalla työkalujen sijaintia ja materiaalien käyttöä voidaan nopeasti tunnistaa parannuskohteita.
Kokeile esimerkiksi "spagettikaaviota": jokainen tiimin jäsen merkitsee työtilan pohjapiirustukseen omat liikkeensä. Tulokset voivat osoittaa, että tarvitaan lisää kierrätyspisteitä tai että työkalukaapit ja siirrettävät työkalupaneelit kannattaa sijoittaa paremmin. Anna koko tiimin keskustella ja arvioida, kuinka työpaikka ja työvaiheet voidaan optimoida.
Tehokas tapa nostaa työmotivaatiota
Työntekijöiden tyytyväisyys heijastaa sitä, kuinka hyvin 5S toimii. Epäjärjestyksessä on sekä turvallisuusriskejä että mahdollisuus ristiriitoihin. Kun tiimi yhdessä tutkii mahdollisuuksia parantaa tuottavuutta, se kannustaa osallistumiseen ja vahvistaa yhteishenkeä.
Älä anna 5S:n muuttua ylhäältäpäin johdetuksi tehtäväksi
Onnistuneen 5S-menetelmän edellytyksenä on tiimityö ja toisten kunnioittaminen, ei pelkästään hyvä johtaminen. Kun kaikki ovat tietoisia odotuksista, se voi vaikuttaa positiivisesti koko yrityskulttuuriin. Työntekijät ovat usein parhaita asiantuntijoita hukan tunnistamisessa työpaikalla.
Lopulta kyse on sekä johtajien että työntekijöiden välisestä sopimuksesta. Kukaan ei halua aloittaa päiväänsä siivoamalla toisen jälkiä, mutta tämä on helppo välttää, jos työpaikka pidetään siistinä alusta asti.
Vaiheittain: 5S-menetelmän käyttöönotto
1. Tee inventaario ja arvioi, milloin kutakin esinettä on viimeksi käytetty, mihin sitä käytetään ja kuinka usein. Päätä, säilytetäänkö se. Poista tarpeettomat esineet, kierrätä tai siirrä pois. Vähemmän tavaroita tarkoittaa vähemmän sekasotkua.
2. Aseta helposti saataville tarvittavat esineet ja merkitse niiden paikat. Ne tavarat, joita käytät eniten, tulisi sijoittaa lähimmäksi. Hyvin järjestetty järjestelmä vähentää odotusaikoja ja turhaa liikkumista. Muista, että myös tiedon, kuten tilausohjeiden ja piirustusten, tulee olla helposti saatavilla oikeassa paikassa.
3. Siivoa säännöllisesti ja huolla samalla koneet ja laitteet. Dokumentoi työpaikan siisteys ottamalla esimerkiksi valokuvia.
4. Käytä tarkistuslistoja, siivousaikatauluja ja ohjeita muistuttamaan, mitä tehdään, milloin ja kenen toimesta. Tämä vaihe on ratkaiseva, jotta uusi järjestys vakiintuu. Tarkista työnkulku ja dokumentoi, mikä toimii ja mikä ei.
5. Ylläpidä ja paranna rutiineja, kun havaitset ongelmia. On hyvä idea laatia yhteinen, pitkän aikavälin suunnitelma, jossa määritellään tavoitteet esimerkiksi vuodeksi, kahdeksi tai viideksi eteenpäin.
5S-menetelmän kuudes askel
Joskus 5S-menetelmään lisätään kuudes ”S”, joka tarkoittaa turvallisuutta. Tämä voi sisältää riskien ja uhkien arviointia sekä työntekijöiden kouluttamista turvallisuusmenettelyissä. Standardoituja tarkistuslistoja voidaan käyttää näiden asioiden säännölliseen tarkistamiseen.
Yhteensopivuus muiden strategioiden kanssa
5S-menetelmä on erityisen suosittu teollisuustuotannossa, mutta sitä voidaan soveltaa ja yhdistää moniin muihin työtapoihin. Menetelmä toimii yhtä hyvin niin toimistopöydällä kuin koko liiketoiminnassa. Koska menetelmä on yksinkertainen, sitä voidaan käyttää yhdessä muiden järjestelmien, kuten Kanbanin tai PDCA:n kanssa.
Yhteenveto
5S-menetelmä koostuu viidestä vaiheesta: Lajittele, Järjestä, Puhdista, Vakioi ja Ylläpidä, jotka yhdessä lisäävät turvallisuutta, järjestystä ja tehokkuutta työpaikalla. 5S-menetelmä soveltuu kaikenkokoisiin organisaatioihin ja on tehokas keino parantaa tuottavuutta sekä työympäristöä. Se on myös yhteensopiva muiden strategioiden kanssa ja helppo ottaa käyttöön vaiheittain.
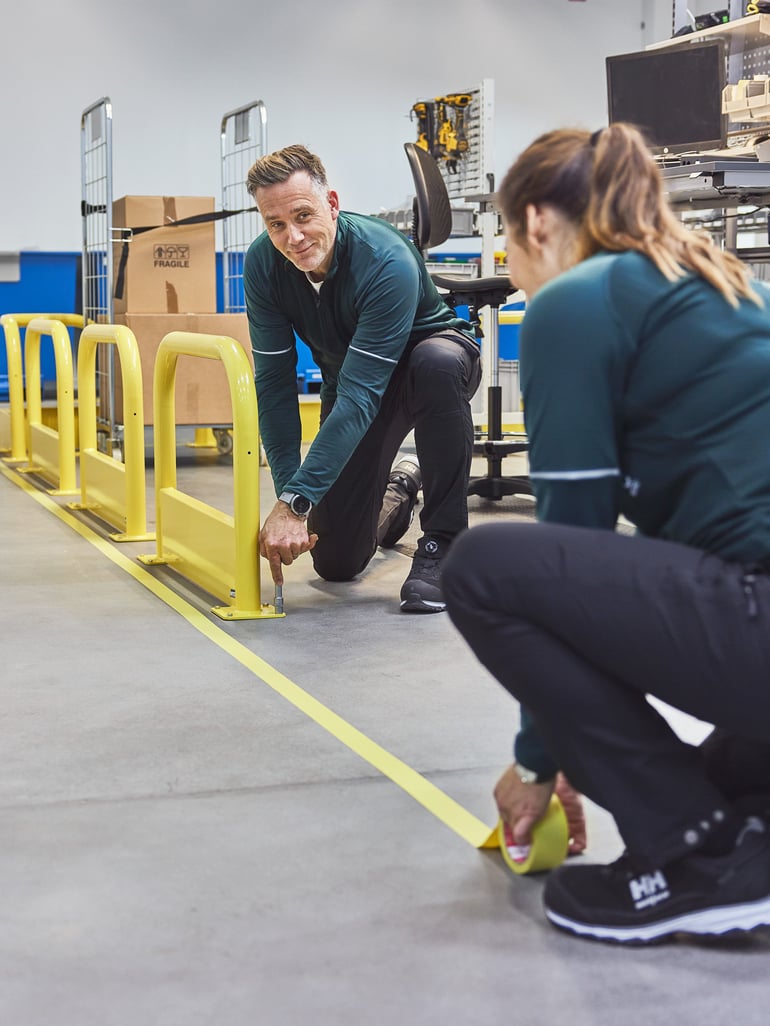